次世代型制御盤設計・製造事例
「制御盤製造の文化を変えた」:日成電機製作所 様
「昔ながらの制御盤の製造現場を改革したい」。この船橋社長様の言葉から、弊社の電線加工機の導入へとつながりました。
制御盤の製造は自動化が出来ないと決めつけており、改革に取り組まない方々が多い中、全国の革新的な経営者が自動電線加工機の導入を実行し、新文化を創出しています。
制御盤の製造は儲かる仕事。是非、作業者の高付加価値化に取り組み、一緒に儲けましょう。
株式会社 日成電機製作所 様
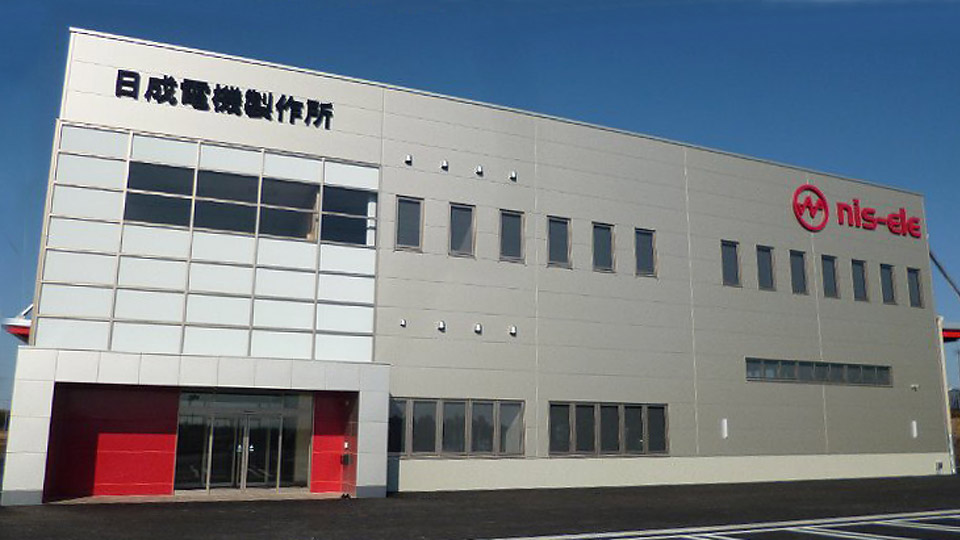
渡部 善政 様
製造部 部長
日成電機製作所様は、電気電子回路、機械装置、ソフトウェアの設計力と、短納期の少量生産から低コストでの量産までに対応する製造力を基盤に、自動機制御装置、搬送装置、検査測定装置、通信装置などの製品製造に参画。ユニット組立、製品生産、設備構築・据付など、様々なニーズに応えられています。
全自動電線加工機「ST-SYSTEM」
全自動電線加工機「ST-SYSTEM」の導入現場では、ハーネスの作成は全て全自動電線加工機が行うため、作業者は自動で製作されたハーネスを配線するだけ。リードタイム短縮&コスト削減、他社との差別化が可能となります。
競合他社への優位性を勝ち取るために
- ライオンパワー:
- 当時、どの様な問題を抱えていらっしゃったんですか?
- 株式会社 日成電機製作所 渡部様(以下、渡部様):
- 以前、制御盤製作においては板金加工まで自動化していたんですが、「板金加工の自動化」は競合他社でもやっている事だったので、それだけでは競争に今ひとつ勝てないといったところでした。
- “じゃあ何をしたら勝てるのか?”という事になるのですが、残るは「制御盤の製作工程の工数をいかに減らしていくか」という事に絞られ、布線表を使っての「電線の加工→仕分け→配線」に取り組んで工数削減を進めていました。
- ライオンパワー:
- 自分も、電線加工機の営業などで客先に訪問するケースも多少あるのですが、中小企業では“職人さんが作業する”という文化が多いなか、御社を見させていただいて「一歩先に進んでいるな」という印象を持ちました。
- 渡部様:
- そんな中、まず改善が必要と考えたのは「電線の加工」工程でした。
- 少しでも効率や品質を良くするためにと、電線の測長やストリップ、マークチューブへの印字や端子の圧着といった個別の半自動機は既に導入していたんですが、結局は人がする作業なのでチューブの入れ間違いや端子の圧着不良などなどが発生し、何とかしたいと常々思っていました。
- ライオンパワー:
- 御社のように大量に電線の加工が必要なところですと、終日にわたって作業者が電線の加工をしているわけですから、不備が出てくるのは無理もないことだったのかもしれませんね。
- 渡部様:
- そんな時に“ライオンパワーに全自動の電線加工機がある”という話を聞いて、「これだっ!」という感じだったんです。
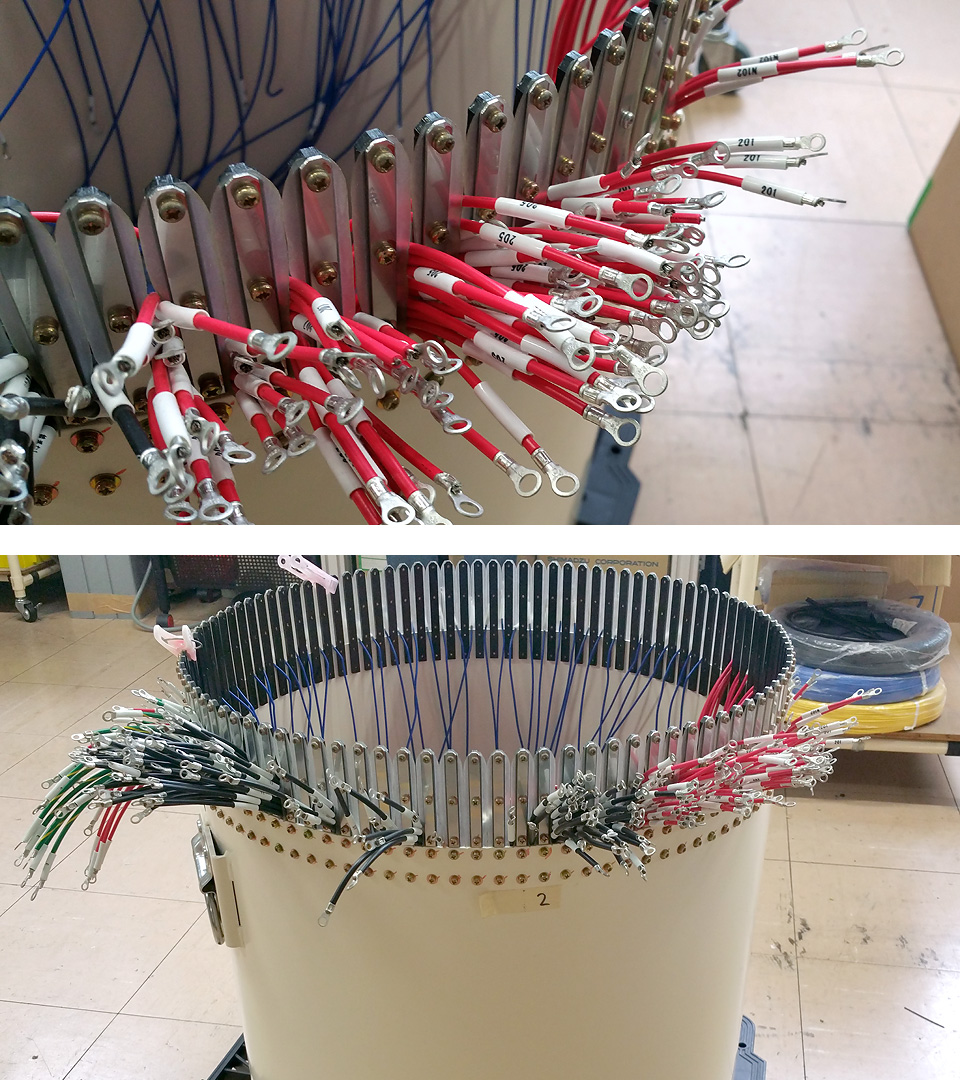
抜きんでていたライオンパワー製品
- ライオンパワー:
- なぜライオンパワー製品を選ばれたのですか?
- 渡部様:
- まずは、なんといってもマークチューブを入れてくれるという点ですね。
- ライオンパワー:
- 確かにその通りですね。それがライオンパワーの電線加工機の最大の特徴ですから。
ただ他社さんでも、特注にはなりますが対応してくれるメーカーがあったと思うのですが? - 渡部様:
- そこで次です。
他社さんの場合はオープン型の端子で、実際に必要なのはクローズ型の端子だったんです。 - もっと言うと、電線やチューブだけではなく、端子も丸端子やY端子など数種類セットしておけば自動でセレクトしてくれる、というライオンパワーさんの装置は魅力的でした。極力人の手が発生する事は避けたかったので。
- またそれ以外にも、他社さんの装置はライオンパワーさんのものよりも価格がかなり高くて、導入には問題ともなりました。
- ライオンパワー:
- そうですね。何しろユーザー様によって使用する端子や電線が違うので、都度カスタマイズする必要がありますから、やはり他社製の物は特注品となってしまい、高額になってしまうようです。
私たちの全自動電線加工機は、様々な要望にそのままでもある程度応えられるような装置としていますので、価格競争力がありますね。 - 余談ですが、過去の最大のシステムは電線の加工機が2台(電線セレクタ、端子セレクタ、チューブセレクタも当然入っています)で収納機が1台というものがあります。電線が20種、端子で裸端子が24種コネクタ端子で8種取り扱いが出来るようになっています。
フレキシブルな対応能力でコストパフォーマンスを発揮
- ライオンパワー:
- そう言えば、立会いの時に「端子を圧着しないものはチューブを入れた状態のまま、電線の先端からチューブが抜けないように出来ないか」という議論をした事が思い出されますね。
- 渡部様:
- 極力、人の作業を入れたくないという事で、電線の自動セレクタ、端子の自動セレクタ、チューブの自動切り替え、端子の圧着ユニットも1.25sq、2.0sqを分けて配置した装置構成としました。
しかし、装置で電線の片側の圧着が出来ない時に、運転モードを変更すると作れるようになったり、また両端圧着できない時には作れないというのが問題でしたね。 - ライオンパワー:
- 最初は一般的に抜け防止の「先端をつぶす」「電線の外皮に切り込みを入れて曲げる」などで実現出来ないかから始まって、全員が装置の前で「あれは?」「これは?」と圧着する箇所を中心に次々に意見を出していたのを覚えています。
- 最後は「“加工を失敗した時に電線を排出するユニット”を改良すれば、電線が曲げられることでヌケ防止にできる」という案で落ち着きました。
- 渡部様:
- その折り曲げ機能が実装されることで、電線全てを装置でながせるようになって良かったです。でなかったら、稼働率も上がらないしPAYするのも大変でしたね。
- ライオンパワー:
- 稼働率といえば、訪問した時に月産本数を集計したことがありますが、MAXの時期で30,000本製作されているのでびっくりしました。装置も1ヶ月フル稼働だったみたいですけど。
以降もコンスタントに20,000本以上は製作されていましたね。 - 渡部様:
- 導入当初は良かったのですが、最近では現在の電線加工機で圧着できないフェルール端子の割合が増えてきて、後処理が大変な状況で困っていたんです。
- そこでこの前、予備の圧着スペースを使ってフェルール端子が圧着出来るよう改造を依頼したわけです。
- ライオンパワー:
- 長期的に考えると、時代の流れで仕様も変わってくる事もあるので、あらかじめ予備スペースを設けておいて正解でしたね!
- ※フェルール端子の半自動圧着機とライオンパワー製のチューブ挿入ユニットを連結することにより、これまで不可能であったフェルール端子にマークチューブを自動で挿入・端子圧着を実現しました。
これにより、丸・Y端子、コネクタ端子(AMP、Molex等)に加えて、フェルール端子が自動加工可能となりました。
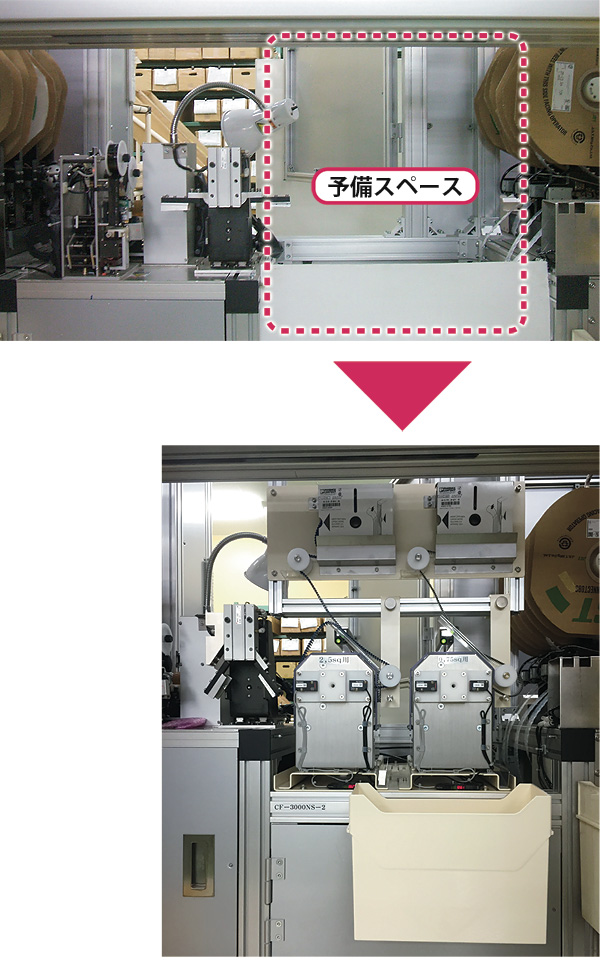
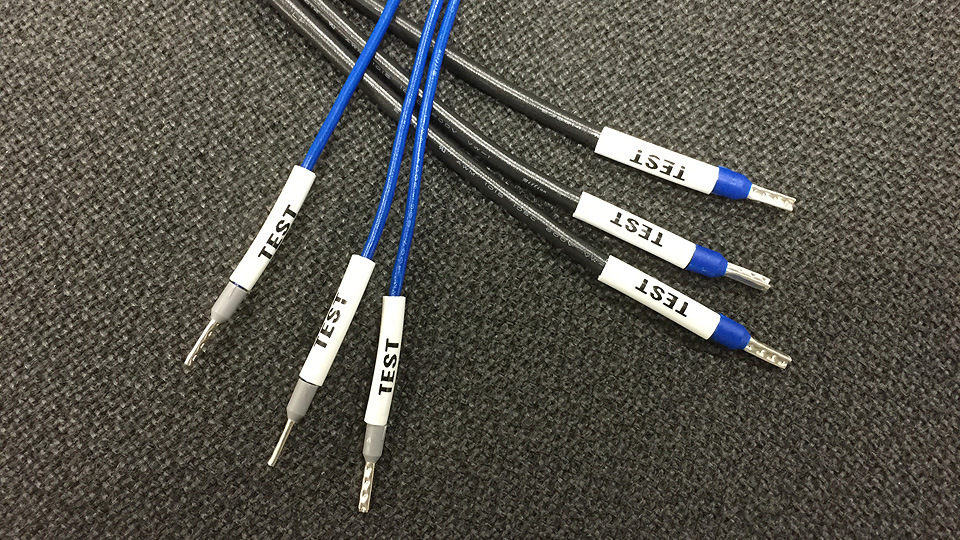
制御盤製造の文化まで変えた電線加工機
- ライオンパワー:
- ライオンパワー社内でも電線加工機を使っており、採算がとれなかった製品も利益が出せるようになっているので、“電線加工機を導入すれば大幅な工数が削減される”という事は分かっているのですが、他に良かったと思われる点はありますか?
- 渡部様:
- そうですねぇ…電線を加工するデータは必要ですが「電線」「マークチューブ」「端子」といった材料をセットするだけで、『自動で材料をセレクトして加工してくれる』というのと『加工された電線の仕分けも出来ている』というのは非常に楽ですね。
- また、購入した電線の巻き状態が悪いとダメな場合もあるのですが、夜間でも電線を作ってくれるというのは便利ですし、装置が加工してくれるので品質が安定しますよね。導入前に電線の加工にあてていた人を配線作業にまわせたりなど、人のやりくりも楽になりました。
- 装置を導入した事で制御盤製作の考え方というか…文化まで変わったかなとさえ思えてきます。
- ライオンパワー:
- 部品手配をしている間に電線の加工もしておけば、部品が揃い次第、部品取付そして配線と、それだけで終わってしまってリードタイムが大幅に短縮できますから、“文化が変わる”とおっしゃるのも分かる気がします。
- 逆に悪い点というか困った点は何かありますか?
- 渡部様:
- まず、気温の変化に弱いところでしょうか。例えば、冬場になって寒くなるとマークチューブがかすれたりするので、マーカーユニット付近を温めたりするのに苦労していました。
- 逆に今、新工場となって空調設備の整った部屋に装置に移設してからは「今までの苦労がなんだったんだ」という感じで安定稼働しています。
- それと電線のメーカーによっては、苦手なものもあるようですね。
後は“チョコ停”が多いなというのが率直な感想です。不思議な事にメンテナンスに来てもらっている時にはよく動くんですけど。 - ライオンパワー:
- よく言われます。でも、メンテナンスで異常な箇所についてはきちんと修正しているからだと思います。逆にちゃんと動いてもらわないと終われないですから…。
その他「次世代型制御盤設計・製造」の主な連携先・納入先
株式会社アイデン 様/アムズ株式会社 様/株式会社キョウデンシステム 様/株式会社三社電機製作所 様/東洋機械金属株式会社 様/平田機工株式会社 様